Large part injection molding is similar to injection molding of parts that are of a smaller size. However, the challenges and complexity scale as the size of the part grows. We’ll explore what is needed to mold very large plastic parts, the benefits and advantages of large part injection molding, the industries that use this process, and tips for optimizing your injection molding process.
Examples of Large Parts Used in Different Industries
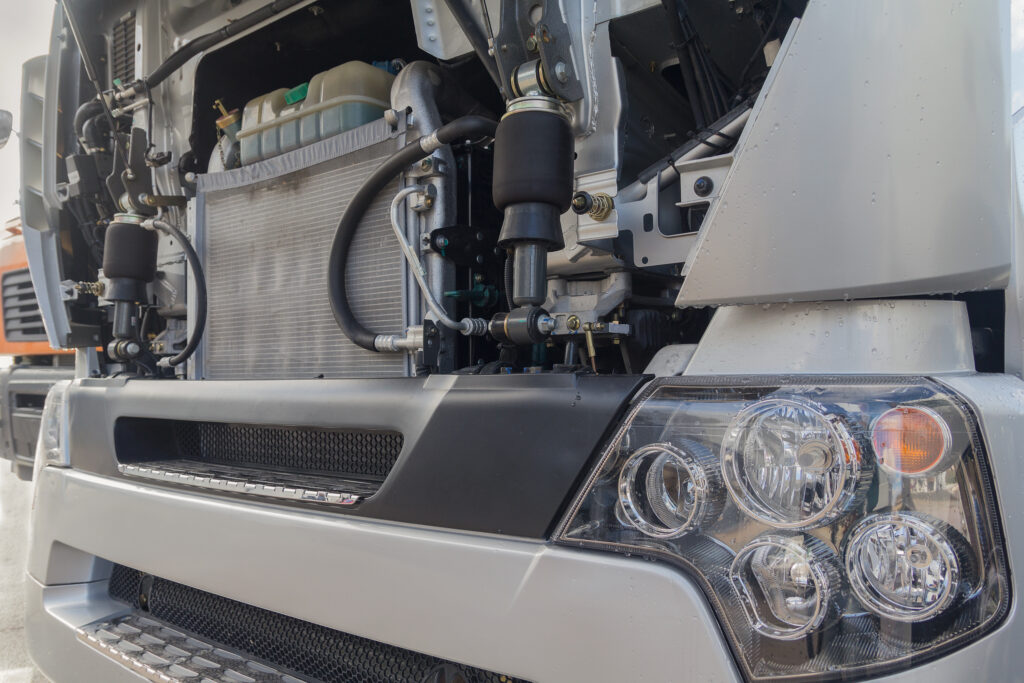
Automotive: Large part injection molding is used in the automotive industry to produce parts such as car bumpers, instrument panels, and dashboards.
Aerospace: The aerospace industry uses large part injection molding to produce parts such as cockpit components and wing components.
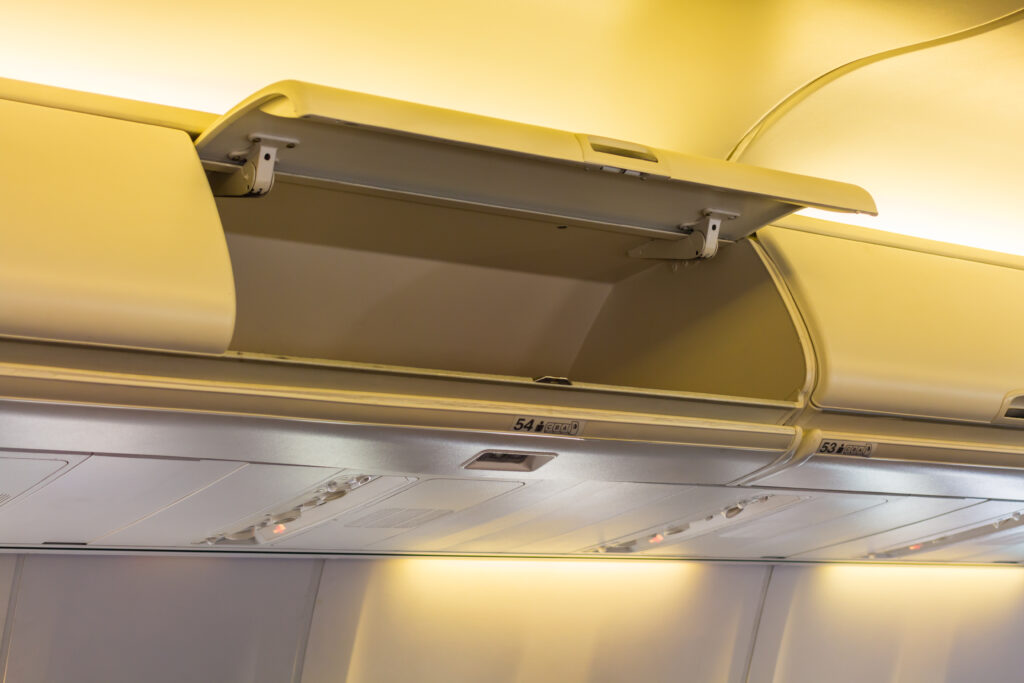
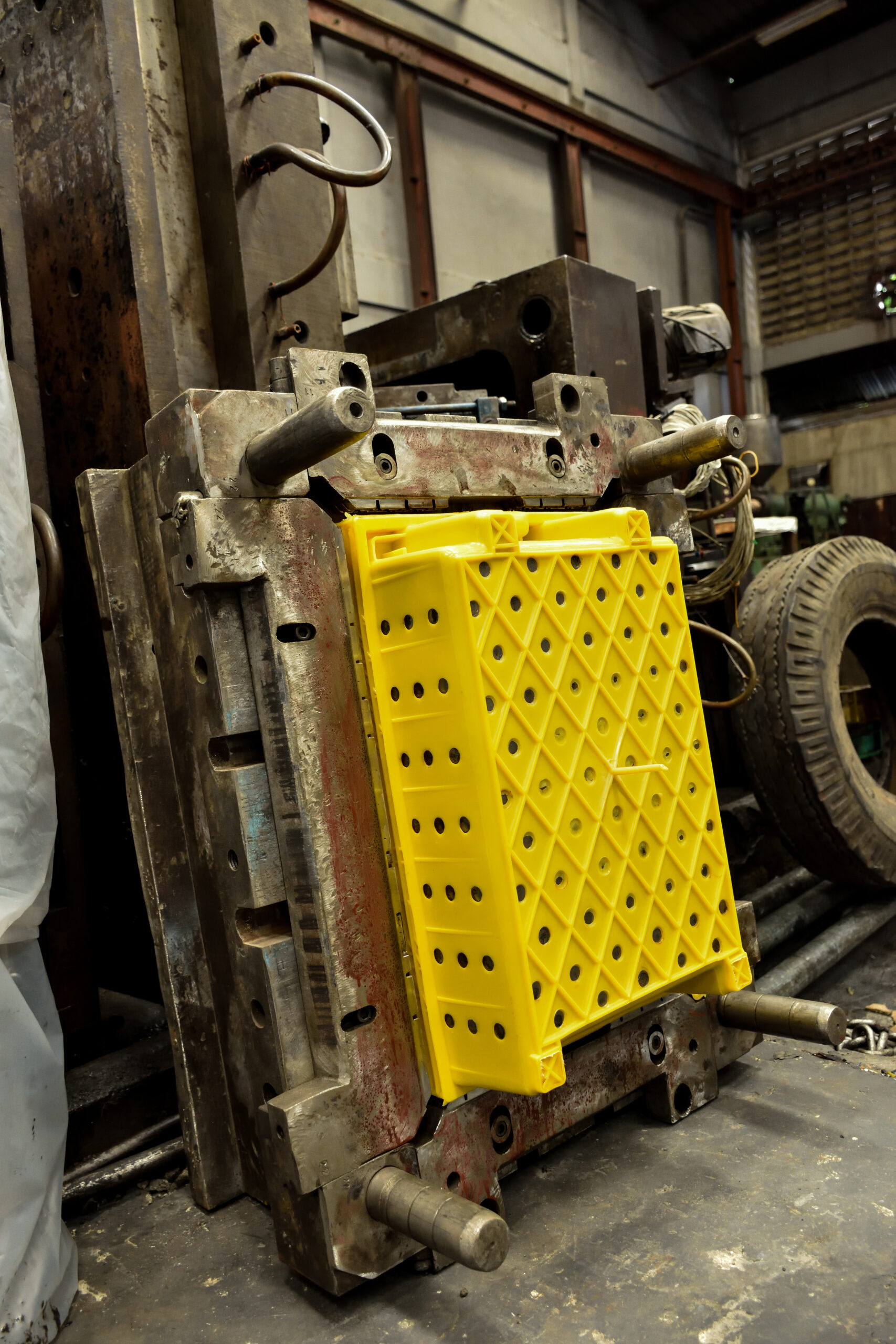
Consumer Goods: The production of large parts for consumer goods, such as containers, appliances, furniture, and toys, is another common use of large part injection molding.
Medical Devices: Large part injection molding is used to produce medical devices, such as imaging equipment, patient monitors, and surgical instruments
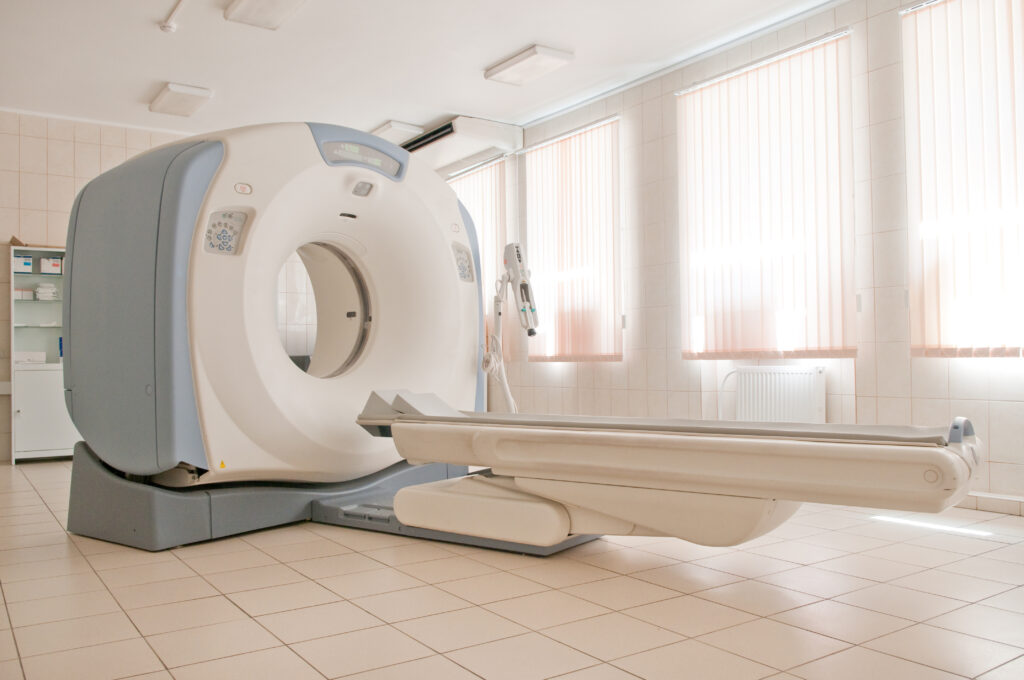
What is Needed to Mold Very Large Plastic Parts
Molding very large plastic parts requires specialized equipment and expertise. Large part injection molding machines are capable of producing parts with a shot size of over 120 pounds and a clamping force of over 4000 tons. The molds used for large parts must be designed to accommodate the size and weight of the part, and the machine must be able to handle the weight and size of the mold.
The process of molding very large plastic parts requires precision and control. The injection molding machine must be able to maintain precise temperature and pressure control to ensure that the plastic material flows properly and fills the mold completely. Additionally, the cooling time required for large parts is longer, and the cooling channels in the mold must be designed to accommodate the longer cooling time.
Design Considerations for Large Plastic Parts
Design considerations for large plastic parts are crucial to ensure that the parts are functional, durable, and cost-effective to manufacture. Here are some recommended design considerations for large plastic parts:
- Wall Thickness: The wall thickness of the part should be uniform to ensure that the plastic flows evenly during the injection molding process. Uneven wall thickness can lead to sink marks, warping, and other defects in the part.
- Rib Design: Ribs can be used to add strength to the part and reduce its weight. However, it is crucial to design the ribs properly to avoid sink marks and warping.
- Draft Angles: Draft angles are necessary to allow the part to be ejected from the mold. Draft angles of at least 1 degree per inch of wall depth are recommended.
- Parting Lines: The parting line, where the two halves of the mold meet, should be placed in a location that is not critical to the part’s function. This will allow for easy ejection of the part and reduce the risk of cosmetic defects.
- Gate Location: The gate is the point where the molten plastic enters the mold. The gate location should be carefully chosen to ensure that the plastic flows evenly through the part and that there are no visible gate marks.
- Undercuts: Undercuts are features in the part that prevent it from being ejected from the mold. It is crucial to design the mold with side-actions or lifters to remove the undercuts.
- Tolerance: Large parts require tight tolerances to ensure that they are functional and meet the desired specifications. It is crucial to design the mold and part with proper tolerances to ensure that the part will meet its intended function.
- Material Selection: The choice of material is crucial for large plastic parts. The material should be able to withstand the intended environment and have the necessary strength, rigidity, and durability.
Working with a good plastic injection molding company is essential for designing and manufacturing large plastic parts that meet the necessary specifications and quality standards. A reputable injection molding company will have experienced engineers and designers who can provide expert advice on the design considerations necessary for producing high-quality large plastic parts. They will also have state-of-the-art injection molding equipment and a well-trained production team to ensure that the parts are manufactured to the required tolerances and with minimal defects. When selecting an injection molding company, it is crucial to consider factors such as their experience, reputation, and equipment capabilities to ensure that they can meet your specific needs. With the right injection molding partner, you can be confident that your large plastic parts will meet or exceed your expectations and be produced in a cost-effective and timely manner.